Computers, Monitors & Technology Solutions
NEW XPS LAPTOPS
Iconic Design. Now with AI.
Sleek laptops with Intel® Core™ Ultra processor and built-in AI – ready for every project.
DELL MONITORS
Dell Monitors are #1 Worldwide for 10 Years*
See everything. Do anything.
WELCOME TO NOW
Learning to Grow with AI
With our smart infrastructure, businesses are cultivating new farming strategies.
Dell Technologies Showcase
Featured Products and Solutions
ADVANCING SUSTAINABILITY
Repurpose. Reuse. Rethink.
Drive change today by exploring our devices designed for sustainability.
NEW LATITUDE LAPTOPS
AI-Enhanced Productivity
Unlock next-level computing with AI PCs and Intel® Core™ Ultra processors.
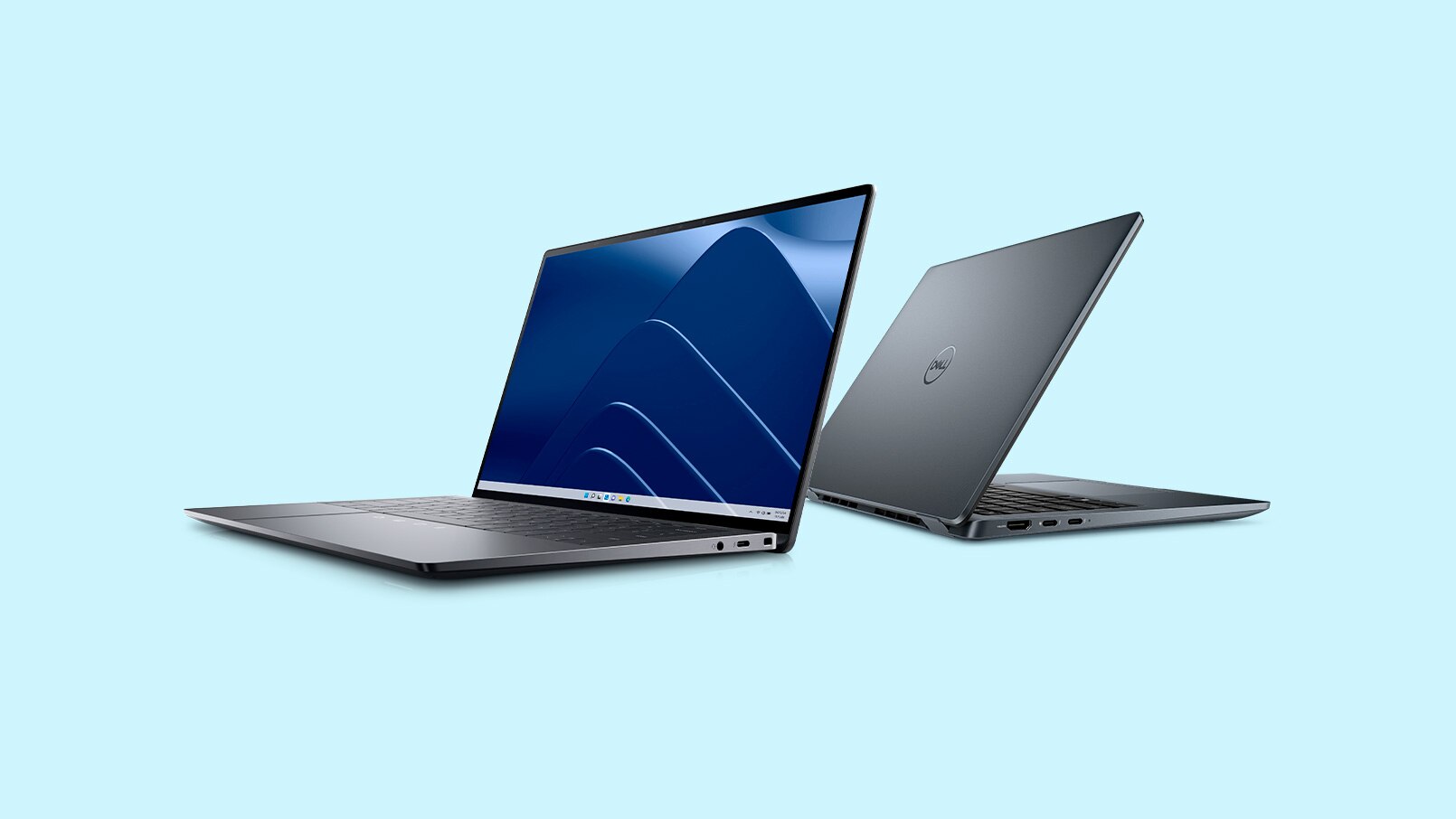
INSPIRON 14 2-IN-1 LAPTOP
Designed for Versatility
Explore with Inspiron 14 2-in-1, featuring built-in AI.
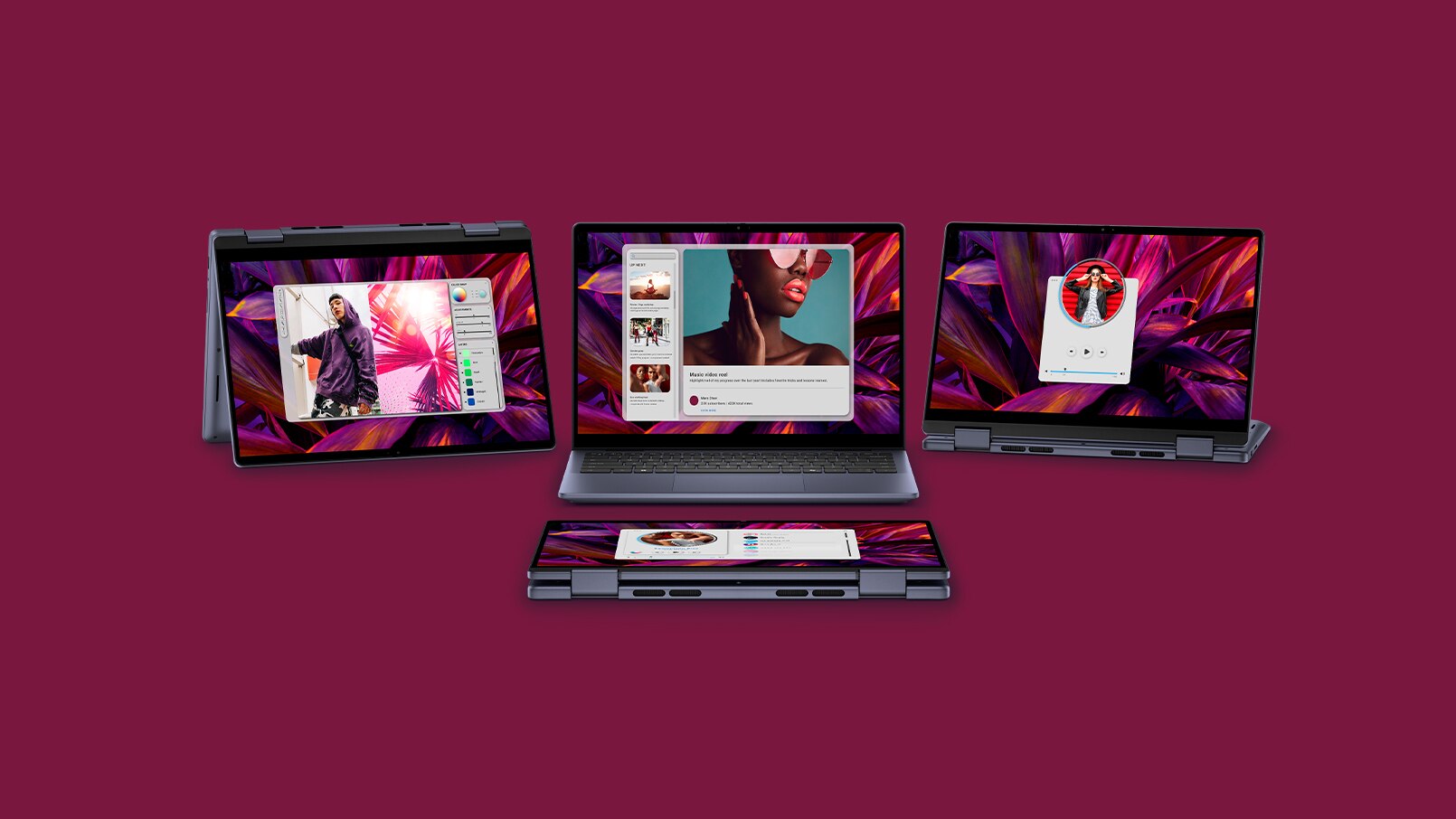
ALIENWARE m18 R2
Stun Rivals. Stay in Awe.
Overpower the opposition with up to 270W of Total Power Performance on our most powerful 18-inch gaming laptop.

SERVERS, STORAGE, NETWORKING
Flexible, Scalable IT Solutions
Power transformation with server, storage and network solutions that adapt and scale to your business needs.
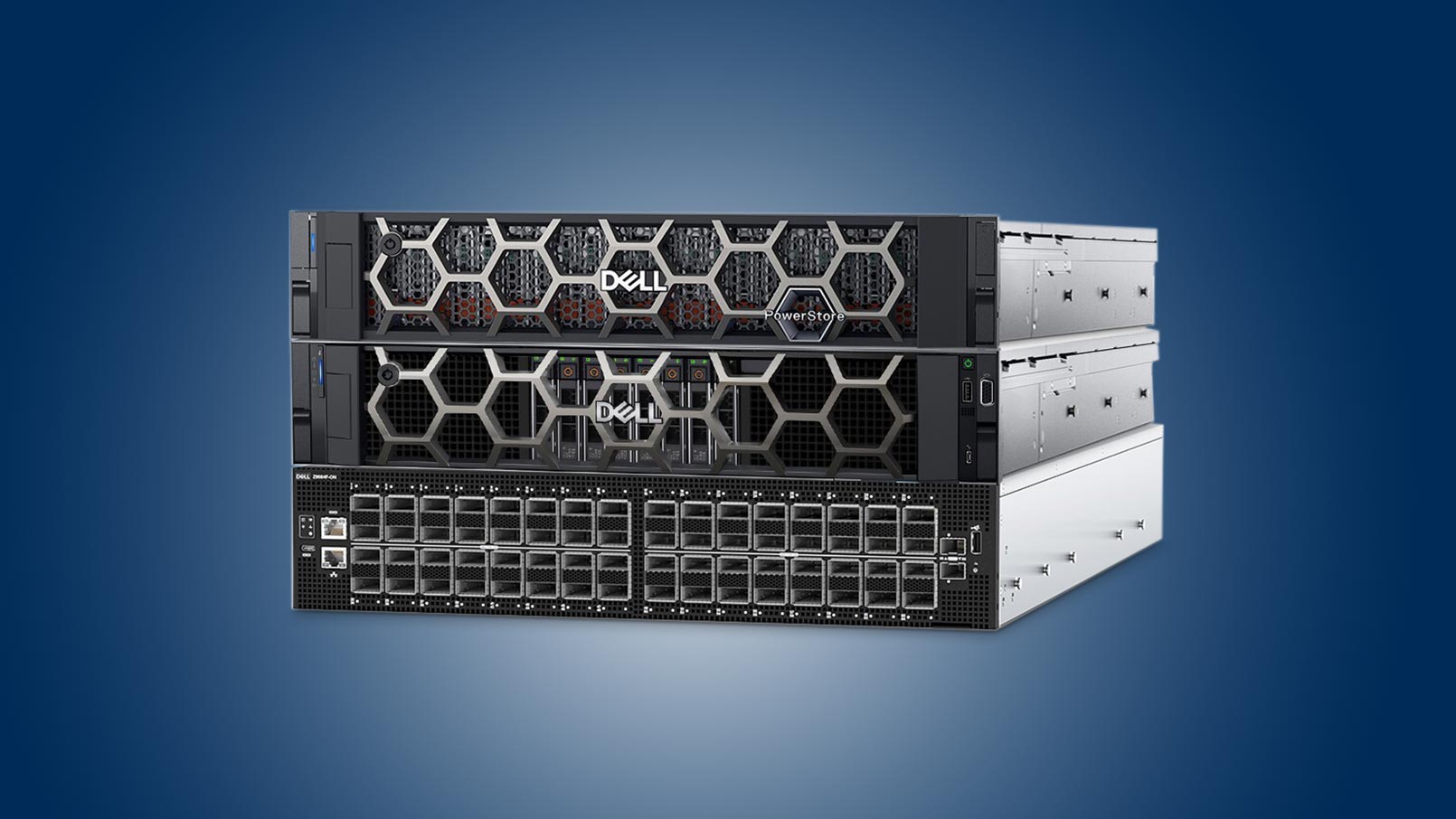
NEW DELL PREMIER WIRELESS ANC HEADSET
Turn Up the Quiet
World’s most intelligent wireless headset in its class* with dual directional AI-based noise cancelling.
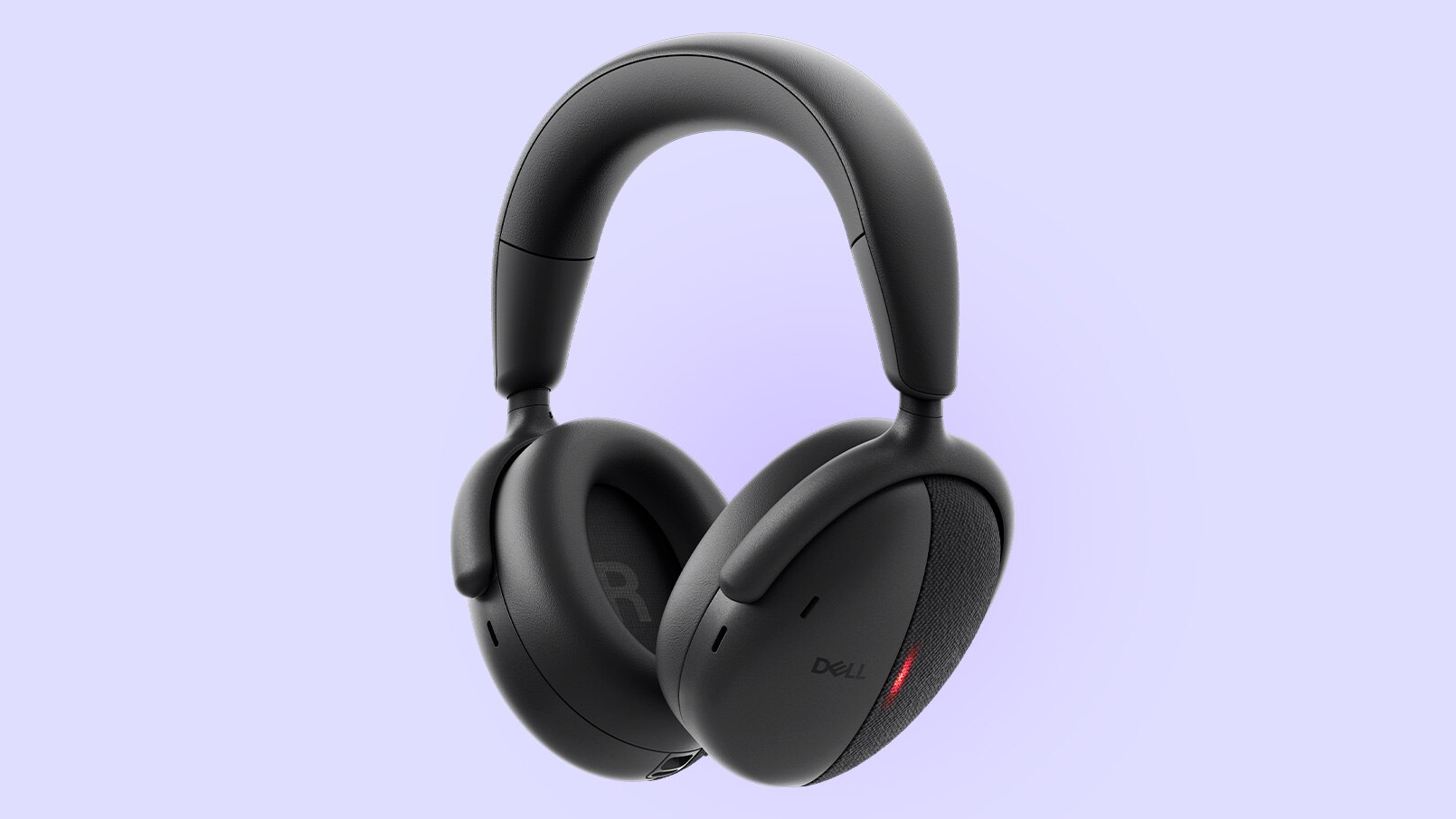
Dell Support
We're Here to Help
From offering expert advice to solving complex problems, we've got you covered.
My Account
Create a Dell account and enroll in Dell Rewards to unlock an array of special perks.
Easy Ordering
Order Tracking
Dell Rewards
Dell Premier
Leverage hands-on IT purchasing for your business with personalized product selection and easy ordering via our customizable online platform.
Simplify Purchasing
Discover Insights
Shop Securely
Latest from Dell Technologies
What's Happening
DELL REWARDS
Shop More. Earn More.