Under ordinary circumstances, a three-bedroom, two-bath house hitting the market would not have landed headlines. But a Riverhead, New York, home made news in 2021 for one special reason: It was primarily constructed by a 3D printer.
3D printing involves digitally designing an object and creating build instructions on a digital file. A printer then follows these instructions to construct a 3D equivalent of the designed object by depositing or extruding material layer by layer. Because the process adds material systematically, it is also called “additive” manufacturing.
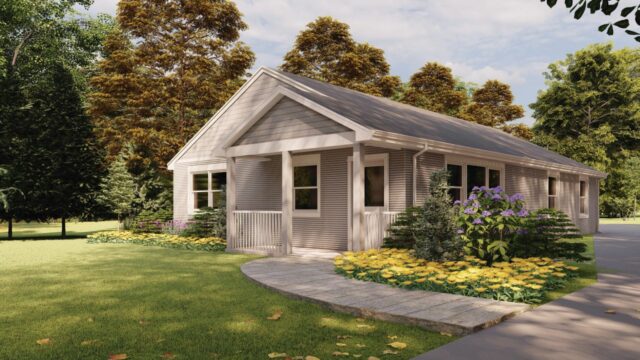
3D printing a home follows these same basic principles: A printhead, operating on a gantry, moves back and forth along a fixed and prescribed track and deposits concrete or other materials of choice layer by layer. As a new layer of concrete is added, the older one cures.
The additive manufacturing process usually prints the interior and exterior walls of the house and utility conduits. Construction company SQ4D, which built the Riverhead home, also prints the concrete foundation. Workers construct the remaining components, such as the roof and rebar, for structural reinforcement and integrity.
Once complete, the houses can be customized on the inside. “The inside of the home can look very similar to traditional [wood-frame] houses in that you can just plaster the wall for a nice flat look,” says Kristen Henry, chief technology officer at SQ4D. “Owners can also choose to preserve the look of the layered 3D-printed lines or have an accent wall in places.”
Meeting demand
The construction industry faces a steep labor shortage: There were 300,000 to 400,000 open jobs in the sector in the fall of 2021, according to the Home Builder Institute. Residential construction accounts for just under half of all industry jobs, and 3D-printed homes might make a dent and help companies do more with fewer employees.
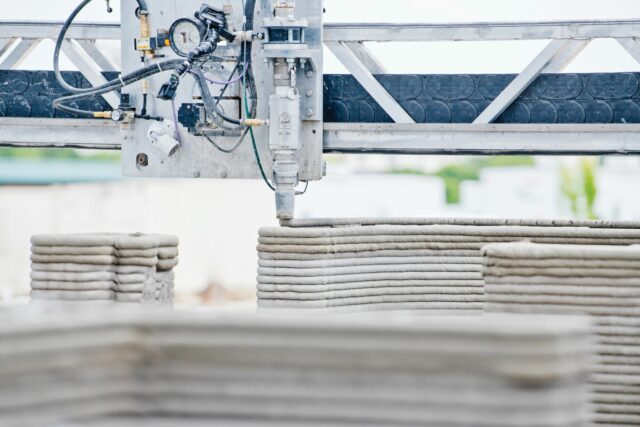
“We are really hoping that this tool can be used to make the work of construction workers easier,” Henry says. “They can work smarter and not harder, since we’re all facing a labor shortage,” she adds. Indeed, labor is one of the many issues that additive manufacturing is looking to solve eventually.
Another advantage: faster turnarounds. The average time to build a home is just over six months and a custom home is 12 months. It took SQ4D approximately 80 hours to print the foundation, and interior and exterior walls for the Riverhead home; the whole process was spread out over 18 print days. Henry is confident that future iterations for a house the size of the Riverhead home will be completed in fewer print days over a span of about 30 days.
ICON, a construction technology company, uses an in-house mobile gantry-style 3D printer called Vulcan, which can print about 500 square feet in 24 hours spread across several days to complete the full wall system of a house. ICON can print two or three homes simultaneously, which further increases the speed of delivery.
An eye toward sustainability
SQ4D’s 3D-printed homes are much stronger than necessary, which equips them to better withstand natural disasters, Henry says. “The requirements for building codes for any concrete used in traditional homes is [that it must withstand pressures of] 3,500 pounds per square inch (psi),” Henry says. The concrete in the Riverhead home withstood more than twice that, she reports.
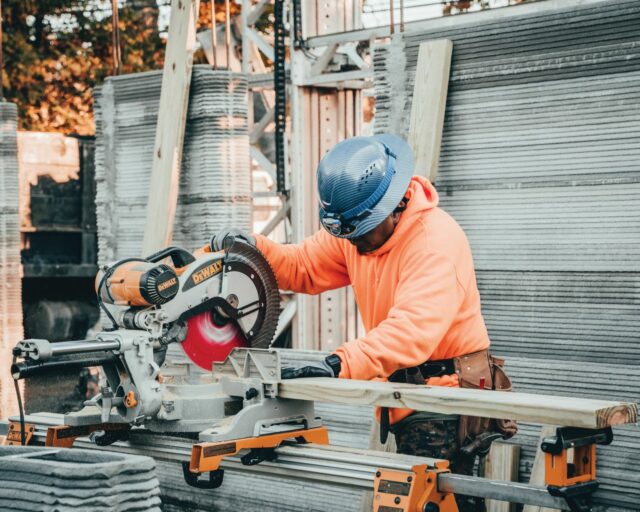
3D printing is precise, using only as much concrete as is absolutely necessary, which helps minimize the net carbon footprint. It also can help create walls with special elements in between the layers that decrease energy consumption. Oak Ridge National Laboratory, for example, is experimenting with techniques to cool walls by piping water lines through them instead of having to rely only on air conditioning in the summer.
A paradigm shift in construction
The advantages of 3D printing homes are mostly due to the construction industry becoming like its cousin, the manufacturing industry, saysPeter Zelinski, editor-in-chief of Modern Machine Shop and Additive Manufacturing magazines, and co-host of “The Cool Parts Show,” a video series.
Traditionally, construction has been like a big manual assembly project onsite: “You bring sticks and bricks and put it all together with power tools,” Zelinski explains. But when you view each part of the constructed unit as a discrete part to be manufactured, the calculation changes. Just as an airplane wing or a mask can be 3D printed, now so can a wall.
“Technologies like 3D printing allow industrialization and systematization to come to a construction site and for the industry to build more sophisticated objects,” Zelinski says. “It’s a little like bringing the factory right to your build site.”
Challenges to overcome
The U.S. starts and completes over one million homes each year.
As of January 2022, ICON has delivered more than two dozen 3D-printed homes and structures across the United States and Mexico. Michael Gauthier, chief of staff at ICON, says hundreds more are on the way, including an entire development near Austin, Texas. SQ4D is planning on more builds and is eyeing multistory buildings—for which it will need a new version of its printer—and commercial construction.
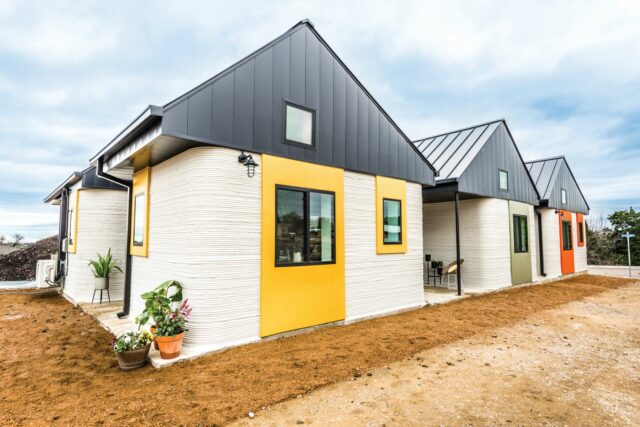
While these two construction companies are by no means the only adopters of additive manufacturing—there are estimated to be about a dozen around the world—the scale is apparent: The number of 3D-printed homes being planned and built in the United States is still only a small fraction of all homes.
However, moving toward the use of 3D printing might be a natural progression in the construction industry. “Improving efficiency is always a primary goal for any company. How do we do what we do better, faster and more profitably? Can 3D printing help us to build a better home in less time? Can it overcome some of the delays that occur in the building process?” asks Rob Krohn, vice president of marketing at Epcon Communities, a home-building franchise company.
The technology is still an emerging concept in construction, an industry that has traditionally been slow to change. “It’s one of the last of the major industries to have an inflection moment, a time when it is forever changed,” Krohn says.
In addition, homes need to be inspected before they can be occupied and, to pass inspection, they need to meet building codes. The problem: There is no standardized code for such homes. For example, says Lionel Scharly, strategic architectural design advisor at Real Estate Bees, an online platform for real estate industry experts, “the ICC (International Code Council) building code does not contain guidance on 3D printing, and [it] supersedes city building codes. As ‘other’ types of construction, it will be subject to city approval.” Construction companies will have to conform to different protocols in different locations.
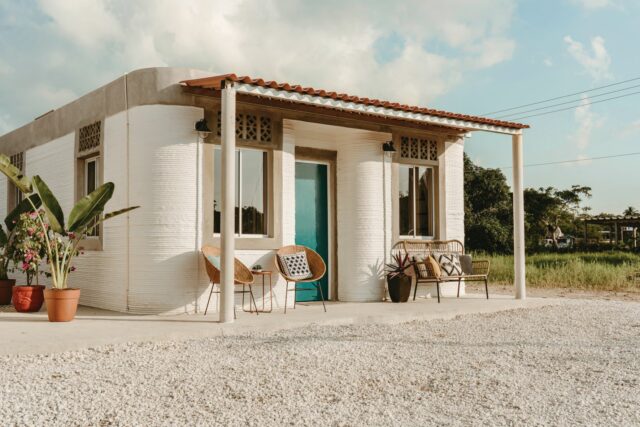
Wrinkles in the 3D printing technology also have to be ironed out. The printhead needs the right material to work with and one that will dry at a rate that will accommodate another layer in a short span of time. “The material is every bit a part of the [3D printing] equation as the machinery,” Zelinski says. “Part of the development of this idea is the pursuit and the formulation of new mixes of concrete that lend themselves to 3D printing.”
ICON uses a proprietary “cementitious material called Lavacrete that can be printed at high speeds while retaining form,” says Gauthier. Meanwhile, SQ4D uses concrete and requires frequent checking for consistency. Though SQ4D’s printer can manufacture single-story homes only, plans are underway to develop printers that can produce even larger structures and possibly multistory units. The largest structure that SQ4D has 3D printed is 1,900 square feet.
“Public perception is always a hurdle with new technologies,” adds Krohn. “Will the public have the trust in a 3D-printed structure? How will it last over time? There is a lot of historical evidence to show the longevity of structures using traditional construction methods. 3D-printed structures will be tested over time.”
Affordable homes?
While a number of factors determine the cost of a home, the high speed and low labor model that 3D-printed homes follow are making them attractive to nonprofits that work on affordable living options.
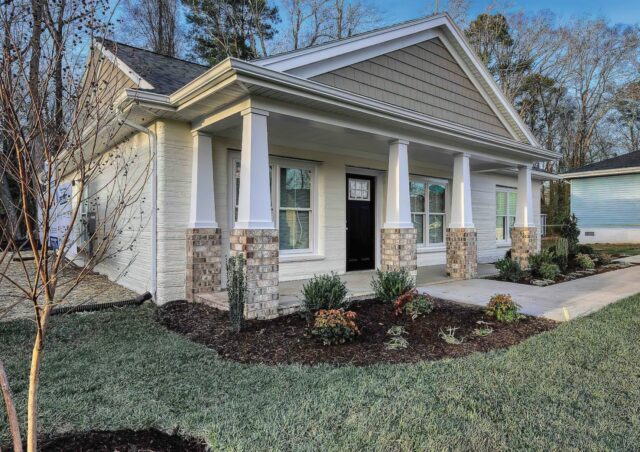
Habitat for Humanity, for example, has had two affiliates build homes using 3D printing technology in 2021 in the United States: one in Williamsburg, Virginia, in partnership with building company Alquist 3D, and another in Tempe, Arizona, using a 3D printer from Germany-based PERI Group. The former is the first 3D-printed home to be owner-occupied; the homeowner closed on her affordable home mortgage in December 2021 with help from Habitat’s homebuyer program, according to a statement from the organization.
Meanwhile, in the southern Indian city of Chennai, affordable, 3D-printed homes are being built by Tvasta Manufacturing Solutions; construction, which can take a little as five days, has also made the structures ideal for natural disaster resettlement. Across the Atlantic, ICON has built 3D-printed homes in Mexico for families living in extreme poverty.
Despite these promising incidents, however, 3D printing may not solve the lack of affordable housing anytime soon. “Using 3D printing technology is one of many new innovations Habitat for Humanity is exploring,” the organization shared. “It is not replacing the way we currently build. We see it as an emerging technology that has the potential to increase our impact on affordable housing.”
Slowly 3D printing a brighter future
“[The growth of 3D printing in construction] requires early adopters to deploy these techniques and early adopters to purchase the homes,” Krohn says. “It really takes the mindset of explorers to go where no one has gone before. To be the first, to try new things. That is how advancements are made in an industry.”
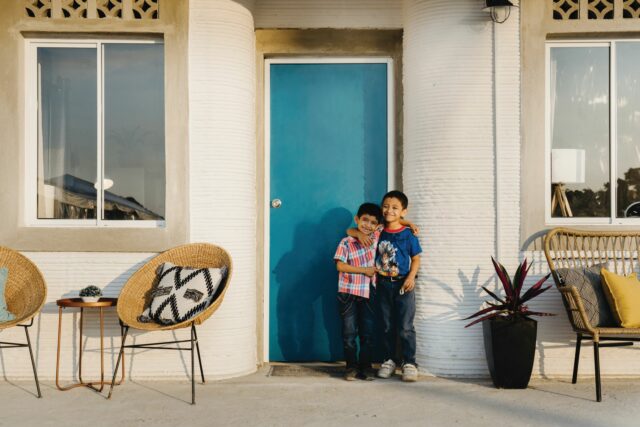
But, in reality, there will be a time lag in incorporating 3D printing and sustainability concepts into the production of actual homes, Zelinski predicts. “We have the technology now,” he says, “but we don’t yet have the mindset and the organization of how construction works to allow us to apply those kinds of ideas in the field.”
Want to read more stories like this? Check out Realize magazine.
Lead photo of 3Strands multi-home housing development in Austin, Texas, courtesy of ICON.